Industrial buildings are a critical component of the American economy. The manufacturing sector is the backbone of America and it’s inside industrial buildings where men and women of this country churn out goods that are used at home and abroad. Any event that temporarily shuts down production in these facilities can have devastating effects on the company, the workforce and the local economy. It is important that industrial buildings are maintained to ensure their safety and integrity.
Industrial buildings come in many different shapes and sizes that will vary depending on the needs of the company and the era in which the building was constructed. Historically, industrial buildings were designed with robust structural systems that allowed them to remain in service for numerous years. Common historical building systems included concrete columns with corbel tops supporting concrete floor slabs; multi-wythe load-bearing masonry walls supporting heavy timber floors and roofs; a combination of steel, heavy timber, masonry, and concrete. In the modern era, many industrial buildings are light-framed steel structures called “pre-engineered” buildings. These buildings are designed and manufactured and sometimes erected by pre-engineered building companies. Pre-engineered buildings are very economical and can be quickly brought into service.
Despite the type of building system used, no industrial building is immune to the wear and tear that takes place over the years of operation. Exposed steel, masonry, and concrete elements may weather requiring periodic maintenance. Heavy forklift traffic inside the building may result in dents, chips, and bowing in walls and columns. Supplemental framing may have been added over the years to support additional equipment or utilities that result in overstressing in the original structure. These are only a few examples of the issues we’ve seen in industrial buildings.
Structural Innovations has evaluated a number of light and heavy industrial buildings. Our experience has identified the following common issues in our building investigations. Please note, these are not all the issues that may occur in a facility, but these are common issues that have been encountered in a number of facilities ranging from food processing plants, pharmaceutical plants, power plants, manufacturing facilities, etc…
- Damaged Columns:
Ask any experienced forklift operator and they will tell you of a column that’s always in their way. Ask any column, and it will tell you its arch nemesis is a forklift operator. Regardless of the type of industrial facility, if there are forklifts or tugs operating inside, there will be damaged columns.
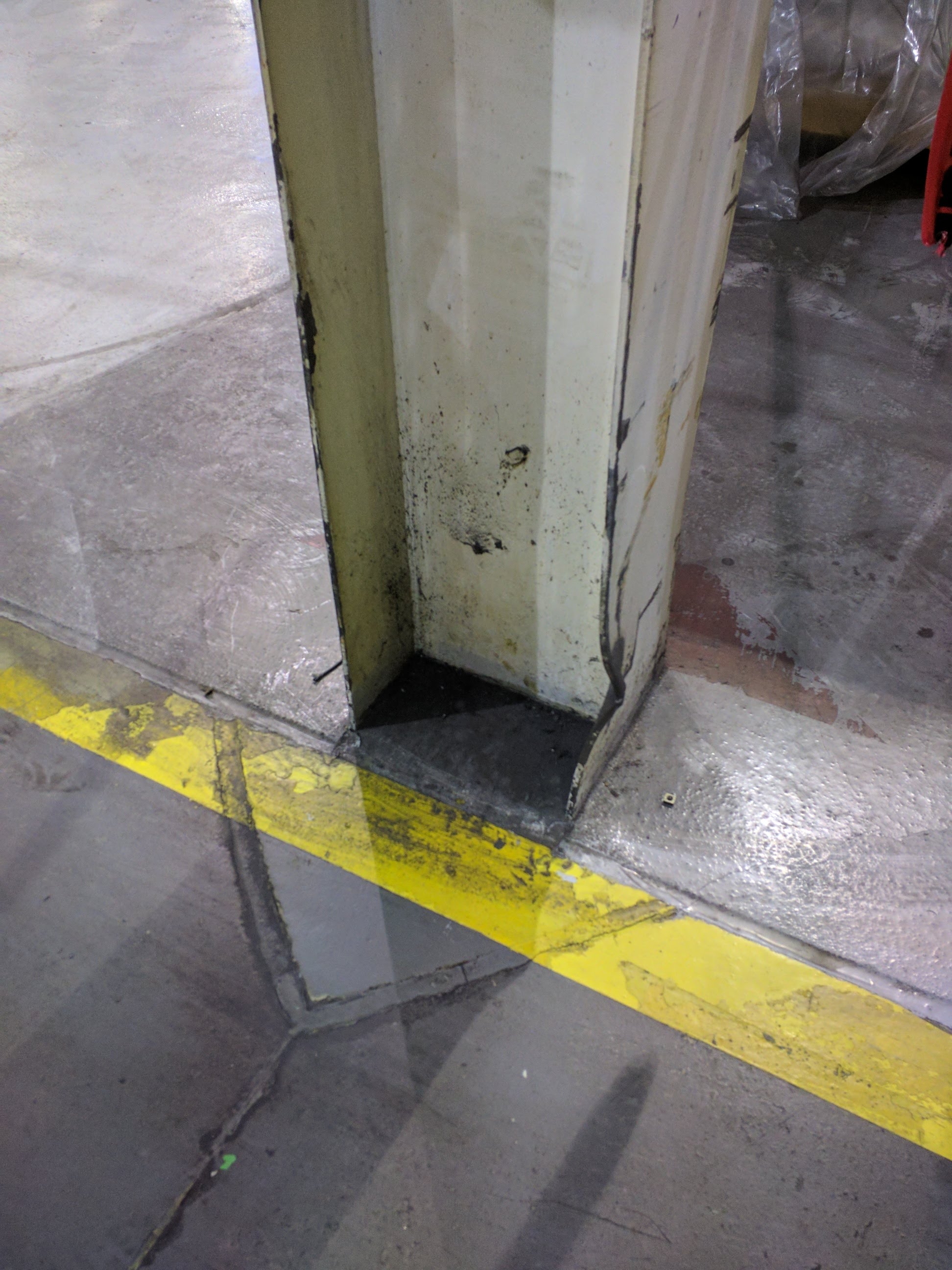
Damage to column adjacent to forklift aisle
- Damaged Walls:
Similar to columns, walls can take a beating inside an industrial facility. Generally, the damage is caused by interior operations. However, we’ve seen numerous examples of damage to exterior walls caused by landscaping operations or truck traffic around the perimeter of the building.
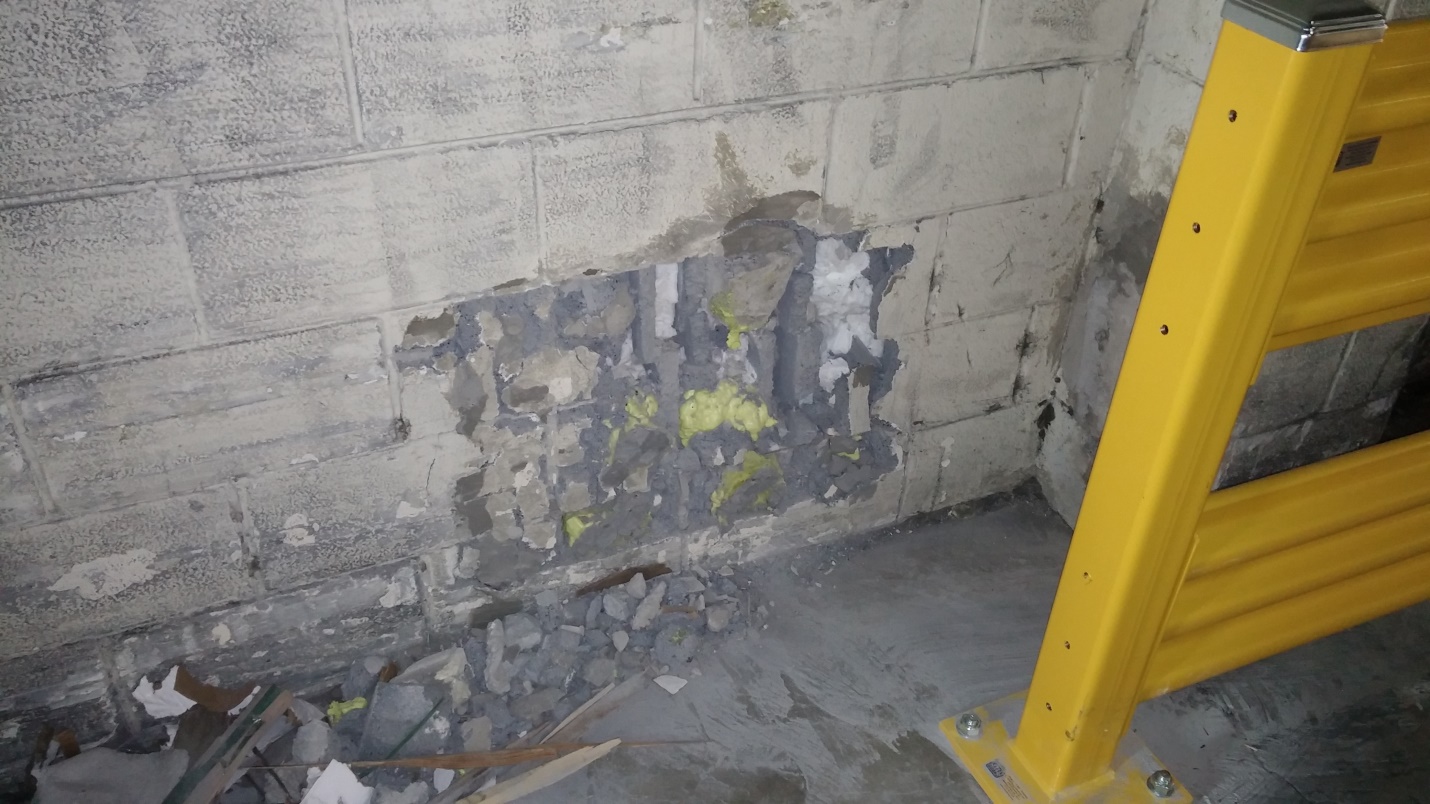
Damage to the wall from forklift
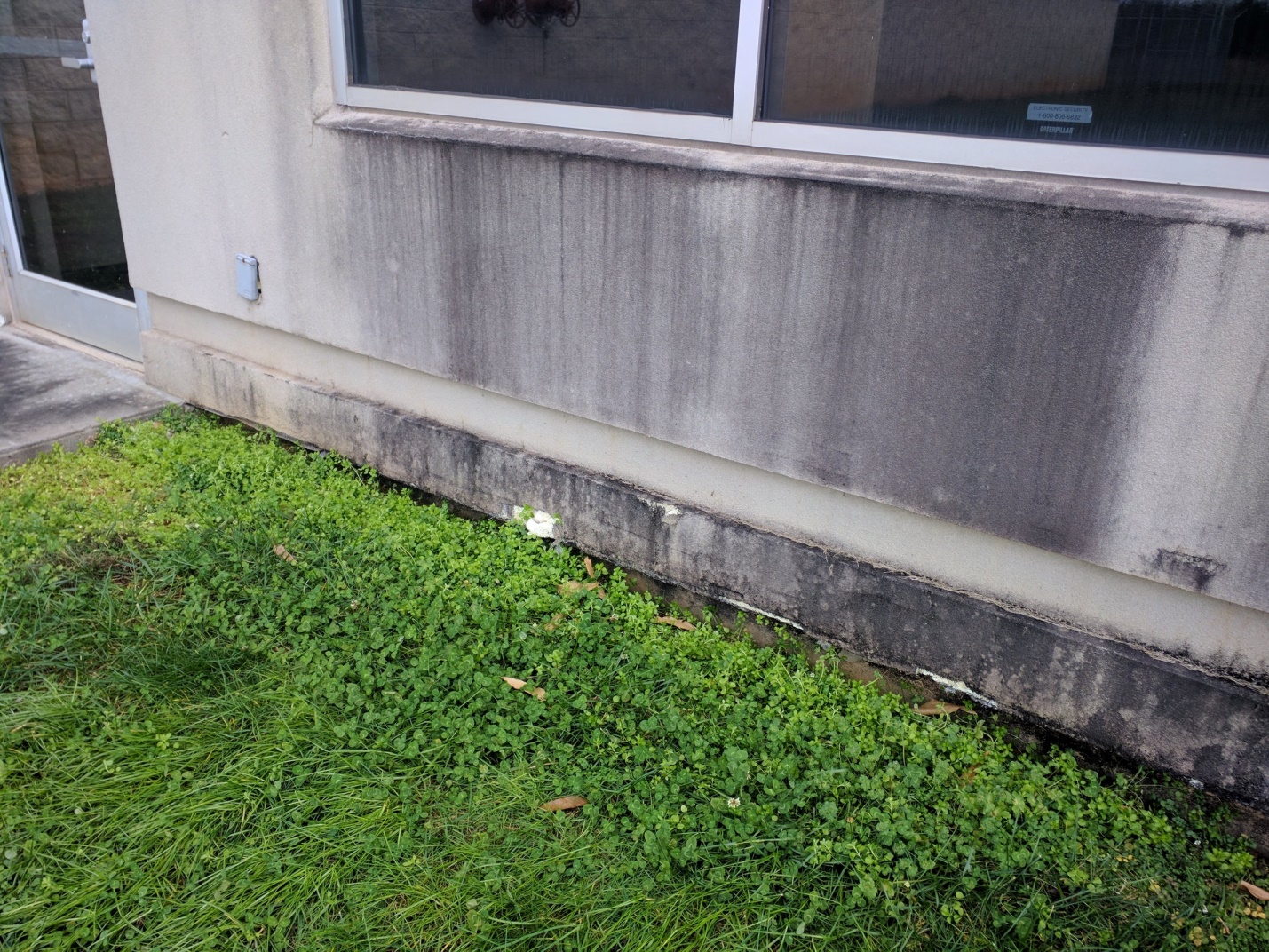
Damage to stucco around the exterior from landscape operations
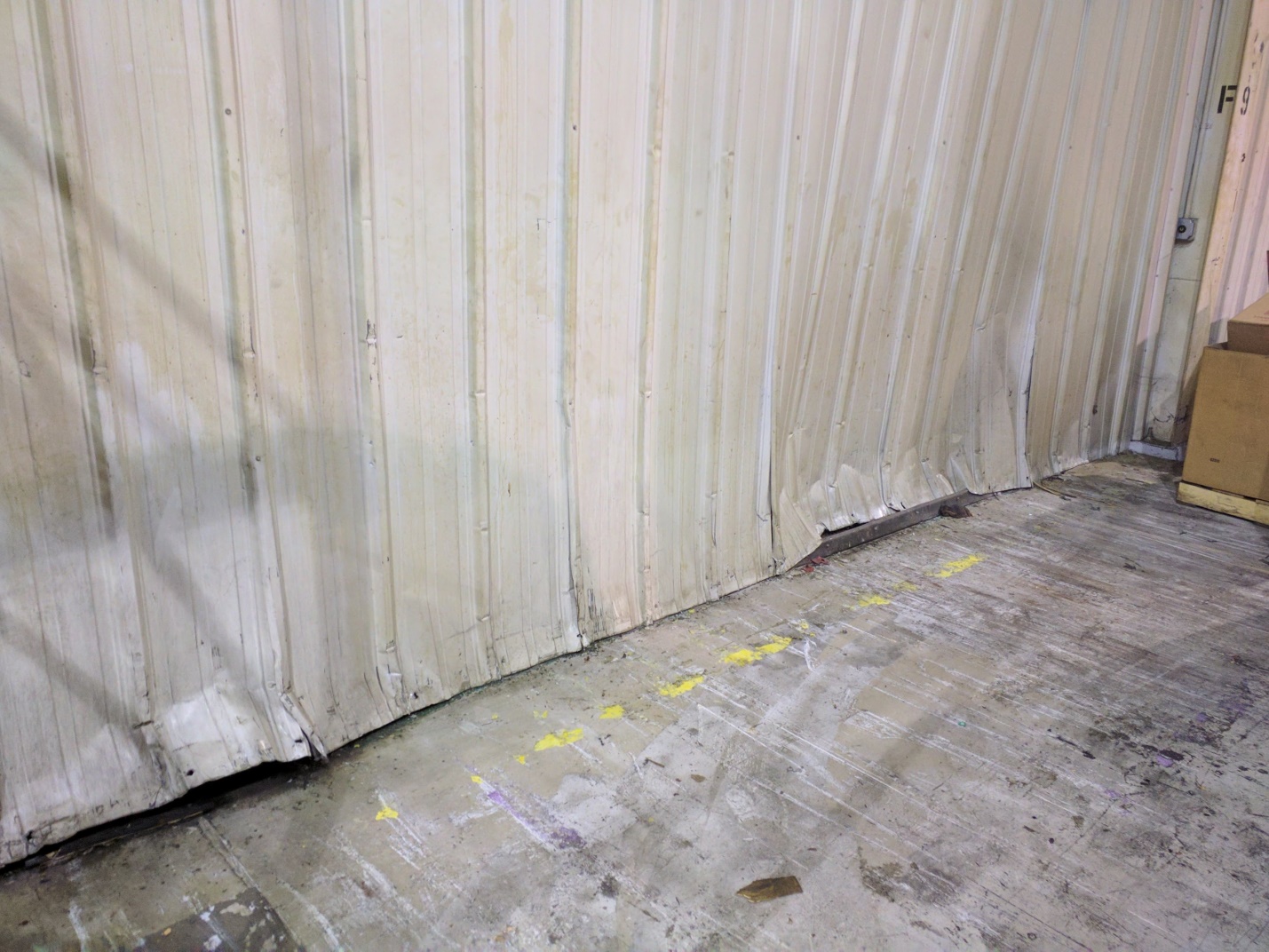
Interior damage to siding from forklift traffic
- Overstressed Framing:
A common myth in industrial facilities is that the framing (i.e. beams, columns, girders, trusses, etc…) can support the world. That is simply not true. Through the years, as the operations inside the facility change and grow, various equipment or utilities are added without regard to the capacity of the original structure. This can lead to overstressing and potential failure in the structure. This overstressing is exacerbated when an individual attempts to cut/chop/notch the original structure.
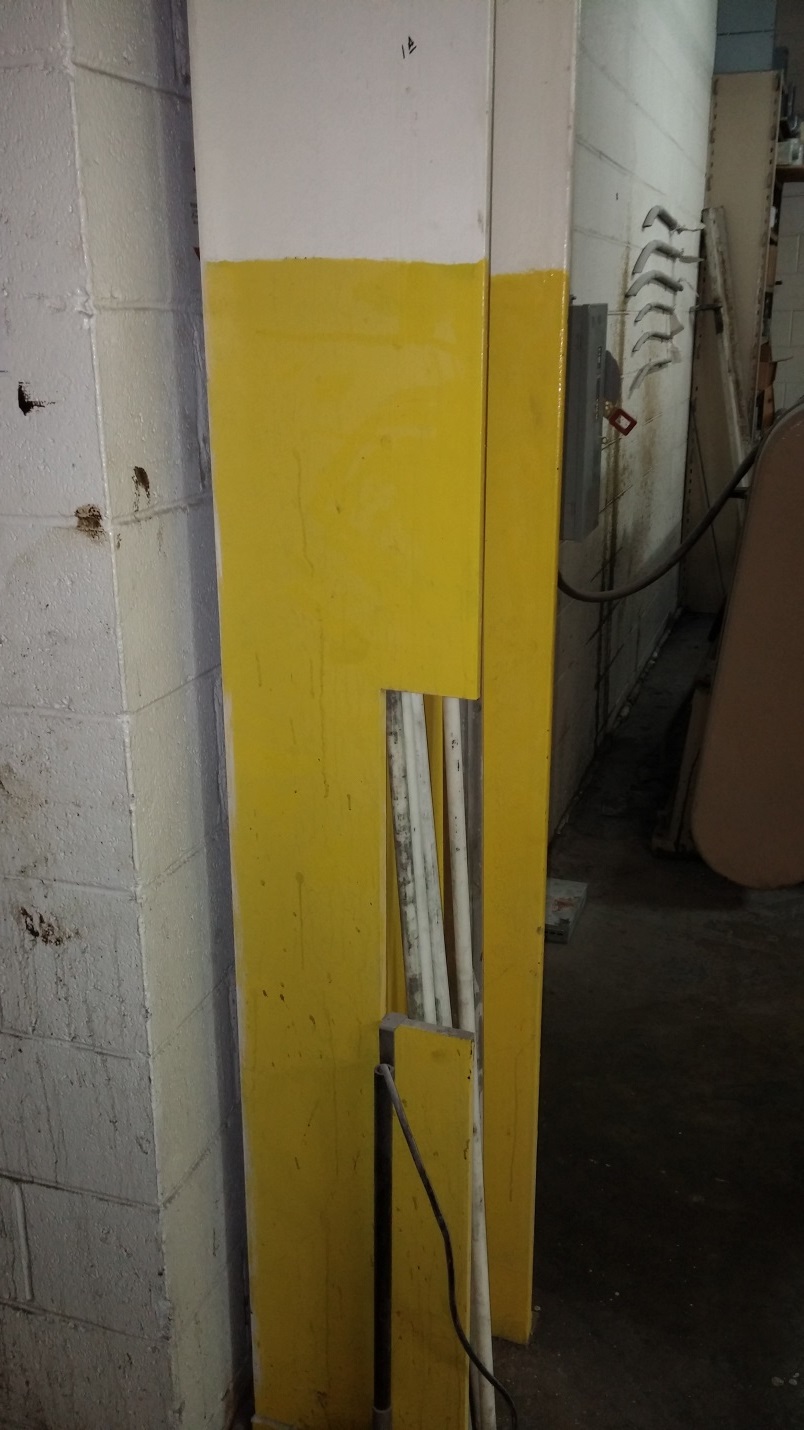
Notch in column
- Inadequate Maintenance of Exposed Structure
The upkeep around the exterior of an industrial facility is key to keeping the building in service. Common issues encountered include 1) inadequate cleaning of gutter and roof drain systems to prevent ponding water on the roof; 2) Coating system on exterior steel is beyond its useful service life or the steel was never coated/galvanized to protect against corrosion and 3) improper maintenance in exposed concrete surfaces.
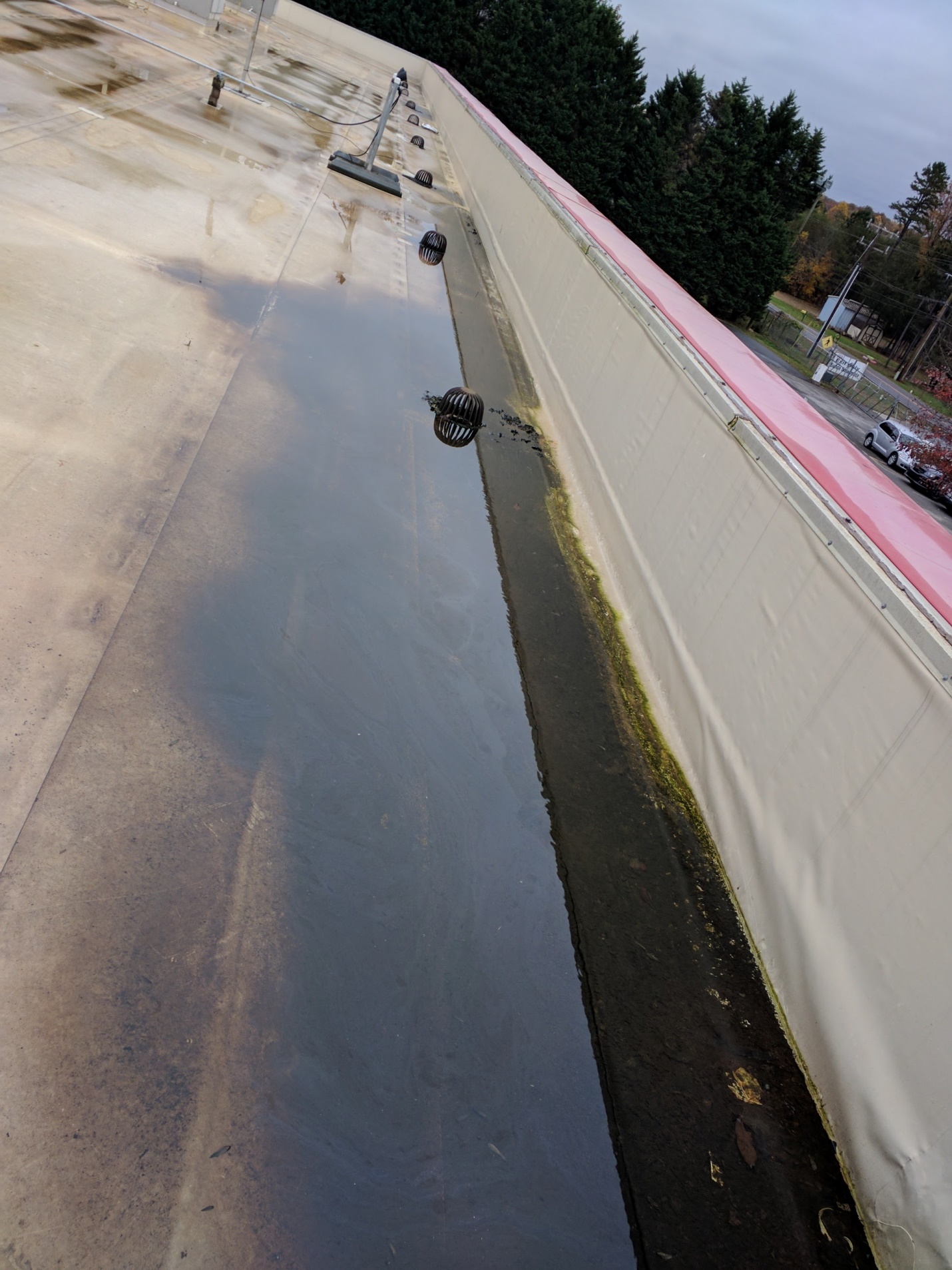
Ponding water on the roof due to a clogged drain
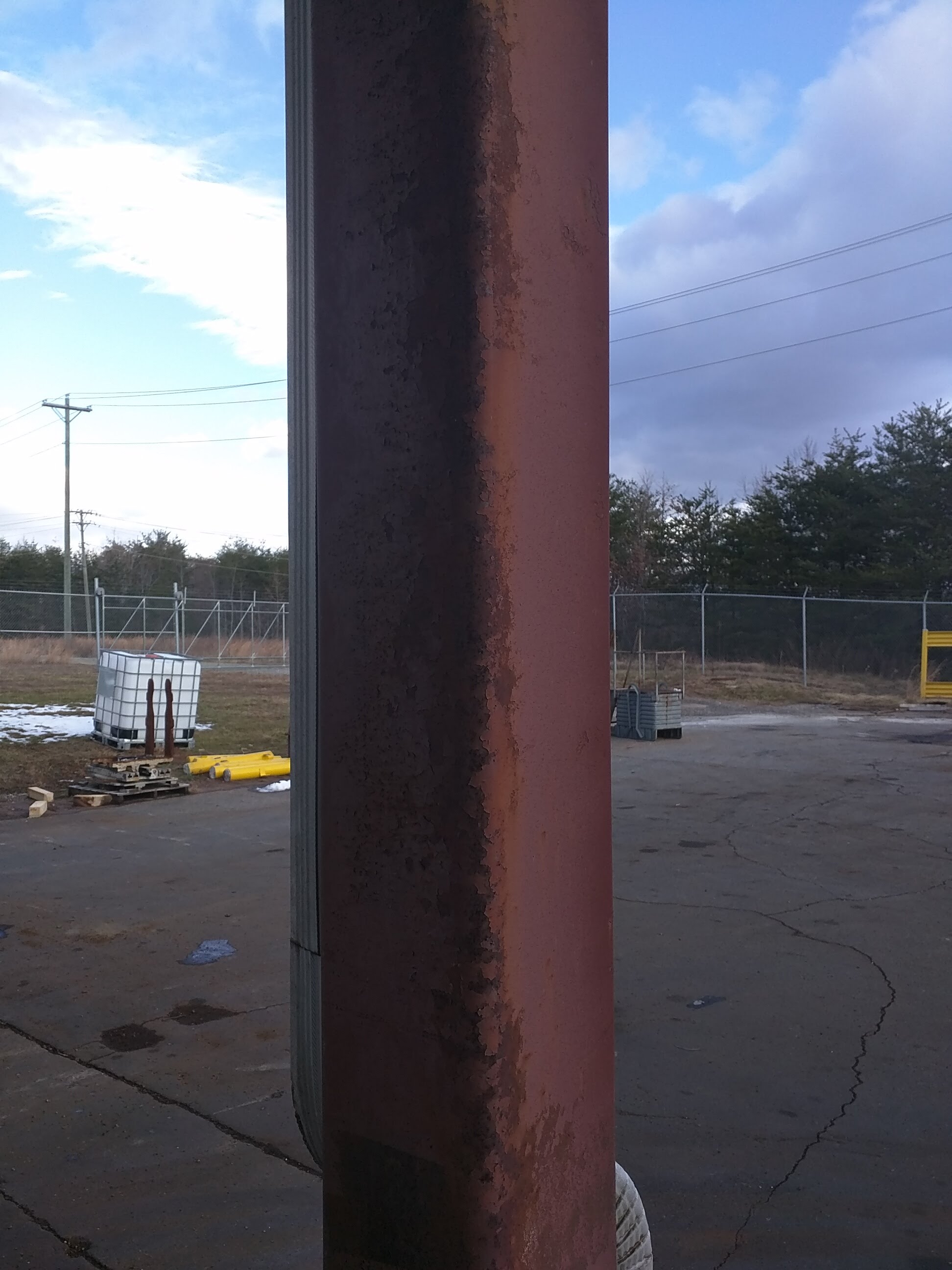
Corrosion on an exterior steel column

Coating system de-bonding from steel
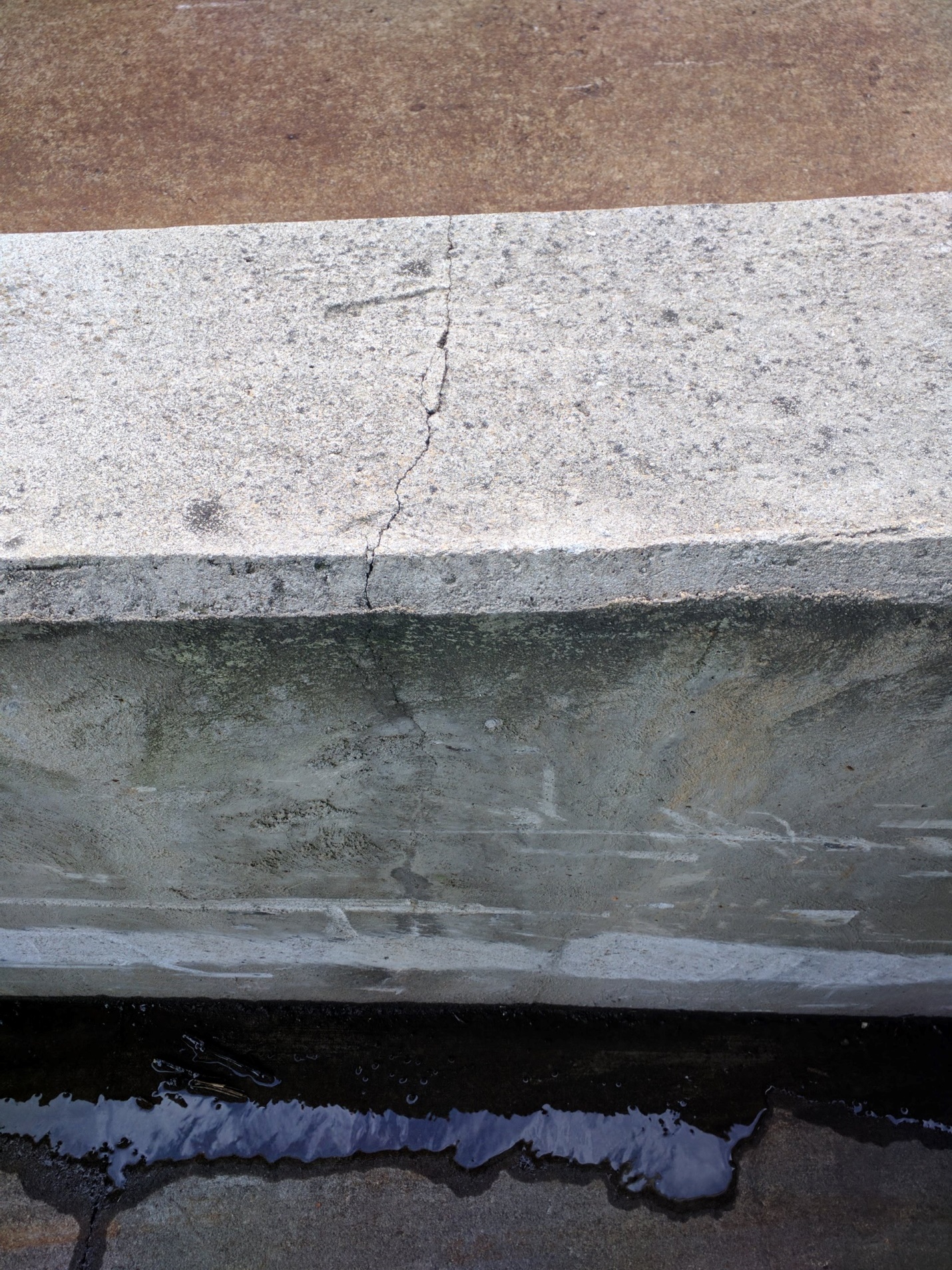
Cracking in loading dock walls
Many of the issues noted above can be addressed through regular preventative maintenance and with the addition of low-cost sacrificial buffers. The following are general recommendations for the common issues noted above:
- Damaged Columns:
Protect the bases of columns using bollards or other sacrificial barriers.
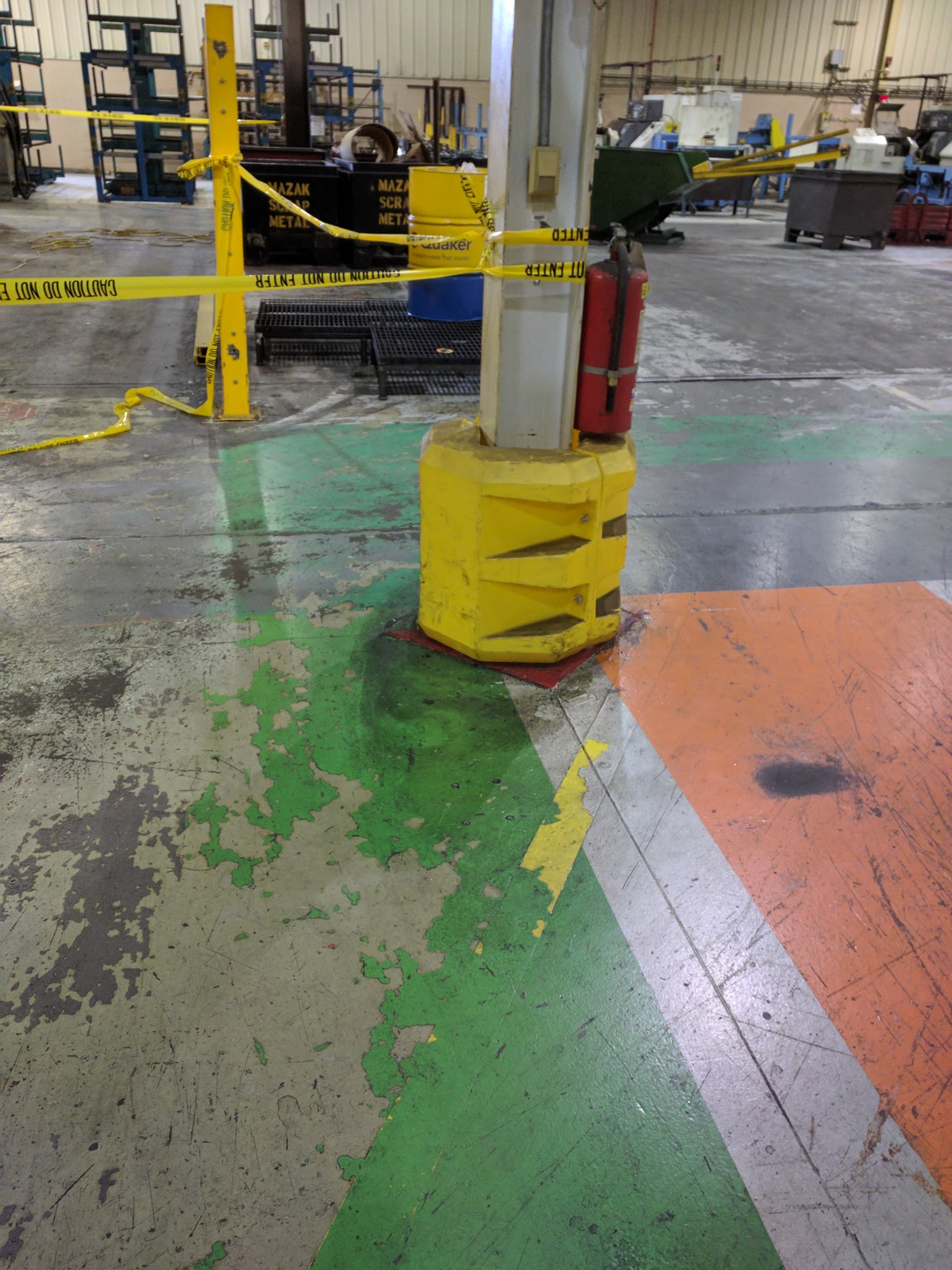
Sacrificial barrier around the column
- Damaged Walls:
Install guardrails along the interior and exterior of walls where forklifts, truck,s or other equipment may be operating. For grassed areas around the exterior, install landscaping that will prevent landscaping equipment from hitting the building.
- Overstressed Framing:
Create a mindset in your employees that all modifications or additions to an existing structure cannot be made without approval from the facility manager. Educate all facilities staff that a structural engineer should be contacted prior to making changes to the building structure. We’ve seen cases where well-intentioned employees added additional framing to a structure that resulted in more harm than good to the structure. Always consult a structural engineer!
Related: Structural Engineering of a Truss Design
- Inadequate Maintenance:
Prepare a maintenance plan that is reviewed periodically and implemented over the course of a year. As the seasons change, exterior maintenance needs may change and require constant evaluation. At a minimum, maintain and clean exterior gutter and drain systems. Clogged drains and guttering allows water to pond on the roof creating a higher potential for roof leaks and overstressed roof framing. We recommend you always consult a structural engineer with regard to coating specifications for exterior steel and concrete elements. If you have areas with extreme corrosion in steel or spalling/cracking in concrete, a structural engineer can evaluate the damage and design the appropriate repair.
This article is intended to serve as a resource to building owners and facility managers. Structural Innovations has performed numerous evaluations on buildings of all types. Please contact us should you have concerns regarding your facility or a facility you’re looking to purchase. We have the ability to review buildings in any number of states where we’re licensed including:
California | Illinois | Texas |
Colorado | Minnesota | Virginia |
Florida | New Hampshire | Washington |
Georgia | North Carolina | |
Idaho | South Carolina |